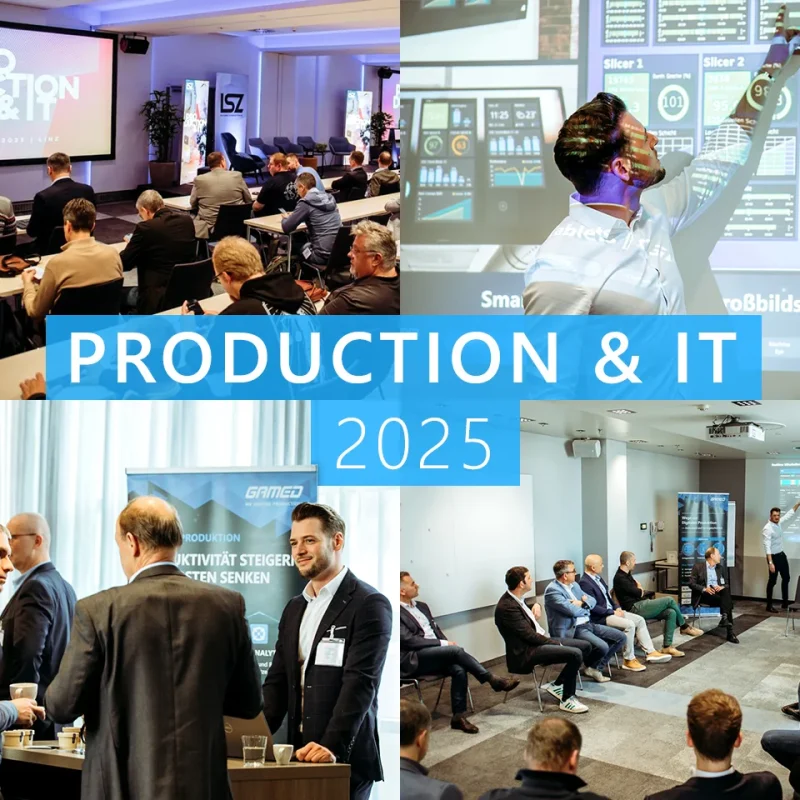
Philipp Seibald
16. February 2024
Check 4.0 is a package in which we work out a roadmap for your transition to digital production – based on analysis of your specific situation. Together we will define the goals. The drivers of digitalisation in production are usually factors such as reduction of waste and stock levels, improving transparency and fulfilment of targets, reduction of paperwork and manual effort in the process, and automation generally.
To get an accurate description of the status quo in your operations we will carry out an assessment of the existing IT structures and the digitalisation level in individual departments. We will evaluate the results relative to reference models and then we will develop a master plan for reaching your goals. Our recommendation will contain carefully designed steps that answer the questions: Where are what data collected automatically? How are the data automatically integrated, evaluated and visualised? What processes are being automated?
If the master plan has the support of top management and the departments, we recommend a bottom-up implementation process: from the machine level to the process level up to the involvement of all the relevant departments.
The first stage is about eliminating productivity killers from the machines and especially from bottleneck machines. The OEE analysis in digital form provides transparency on all the important performance parameters of the machines and shows where potential exists to achieve controlled, predictable processes.
Once the machines are running steadily at the required performance level, the next step addresses the control and optimisation of the whole production process. This is done by means of order-based or piece-based material tracking. The next step is to integrate supporting activities such as quality assurance, tool making, logistics and maintenance into a common information network. This enables coordination of the operational procedures and the analysis of process and quality data in order to understand and prevent errors and breakdowns.
Visualisation in the workplace is an important step towards lean culture and process mastery. Large shop-floor displays and mobile devices give managers access to current indicators and important developments in the processes.
Machine Eye and Cross Plant Reporting System are web-based software systems that allow you to create your own info boards and data cockpits. Data are gathered from external IT systems via open interfaces and displayed in real time on smartphones, tablets or computers.
Automatic analysis of the productivity and performance indicators of your machines and production lines is a central step towards improving efficiency. It reduces the workload on your workers and delivers exact results in real time. Different views support users at different levels in the organisation: from the data of a particular shift to management information and on to cockpits showing information across multiple factories.
The OEE Analyser is a system for gathering machine data in order to calculate the productivity and performance indicators of your machines and production lines. It can be used on any kind of production system, from individual machines to complete production lines or batch processing systems.
What is the status of the manufacturing orders and will they be completed on time? Order tracking provides an up-to-the minute digital picture of the manufacturing process. How far has the job progressed? Which order or which part is currently being processed on a machine? What material is where? Process Master is a framework that enables you to manage and track your orders in an integrated manner. It can receive orders/jobs from the ERP or planning system and add information such as technical instructions or testing instructions. The order tracking visualises the process for the production supervisors, delivers data on results to the ERP/planning level and guides the flow of materials and the transfer of specific programmes to the management level.
If needed, we can also provide solutions for detailed production planning.
Get new insights, demonstrate quality, identify causes of errors and breakdowns – process data and analytics contain a lot of potential. Process data derived from machines, products or quality controls, as well as consumption data are logged in control or SCADA systems. The first stages of data analysis are to gather data from distributed systems, to process them, save them and aggregate them.
DataBridge is a programmable communication system that integrates diverse control and IT systems based on OPC, TCP or at the database level.
Visual DataXplorer is a data analysis system. With an intuitive user interface and carefully selected analytical methods, it enables users to create useful insights into processes quickly and efficiently. With our experience of data analytics frameworks such as R and Python, we will give you all the support you need to make it work in your application.
Going beyond the extraction of new insights into existing processes, the next level is to use data-driven models to control machines and processes. This is done using IIoT platforms and Edge devices.
In times when human resources are at a premium, companies may struggle to keep infrastructure intact and to keep machine availability up. Also, certified companies (e.g. under IATF 16949) have to record and demonstrate their service activities in detail and at regular intervals. IPC helps you to implement TPM optimally and to fulfil these requirements. New technologies such as mobile devices help service technicians working on machines, in the workshop and in the stores.
Philipp Seibald
Head of Business Development