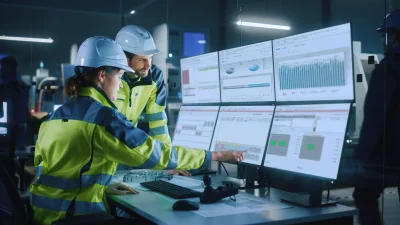
Data and Error Analysis
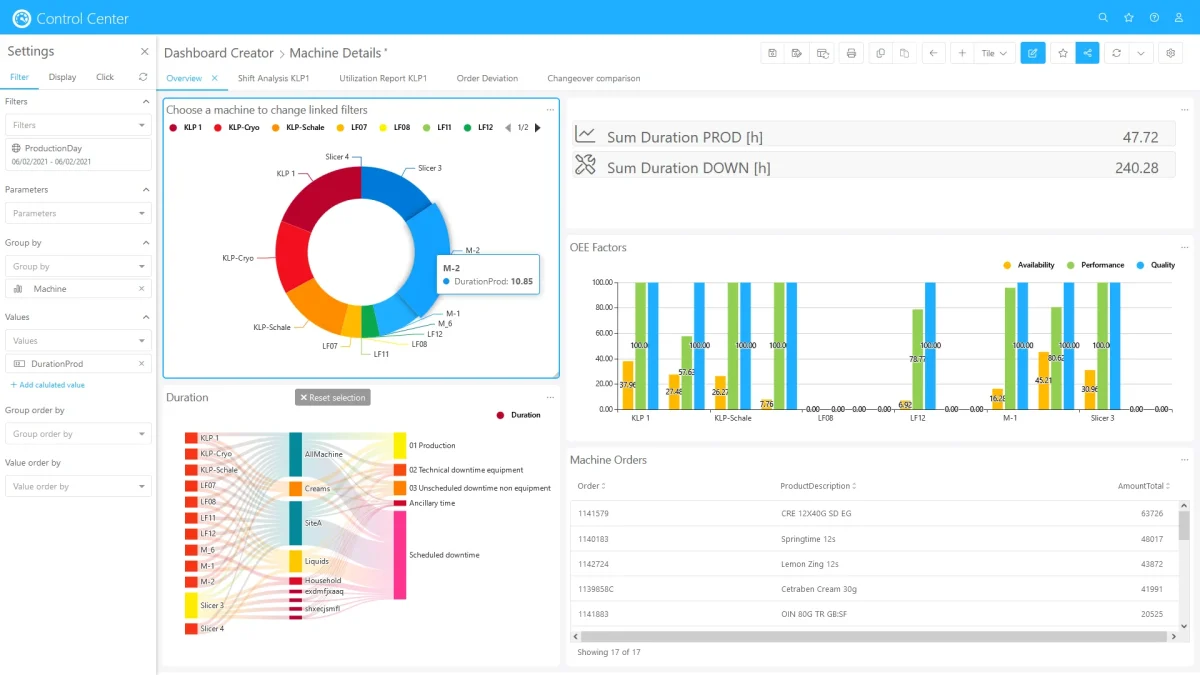
Opportunities and Challenges in Production
Data and error analysis helps optimise production processes and identify error sources early on. One challenge lies in processing large amounts of data from various sources to gain meaningful insights. Real-time analysis, AI-supported methods and statistical procedures are essential for detecting anomalies and deriving appropriate measures. Furthermore, integration into existing systems requires seamless networking of machines, sensors and IT structures. The goal is to increase quality, minimise waste and maximise efficiency.

Benefits of Systematic Data and Error Analysis
Systematic data and error analysis improves production through more precise error detection, reduced downtime and higher quality. Real-time analytics enable rapid responses to deviations, while AI-supported processes support long-term optimisation. Companies benefit from lower scrap rates, more efficient resource utilisation and improved overall equipment effectiveness (OEE). Furthermore, transparent data analysis facilitates continuous process improvement and contributes to predictive maintenance, thus minimising unplanned downtime.

Functions and Features
- Early error detection
- Root cause analysis
- AI-supported analytics
- Dashboards and reports
- Downtime and scrap analysis
- OEE per product/order
- Processing time analysis
- Setup time evaluations
- Machine status overview
- Correlation analysis
- Seamless MES integration

“Only those who understand their data can minimise errors and improve processes in a targeted manner.”
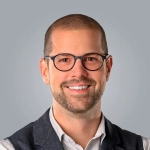
Martin Stimpfl CEO
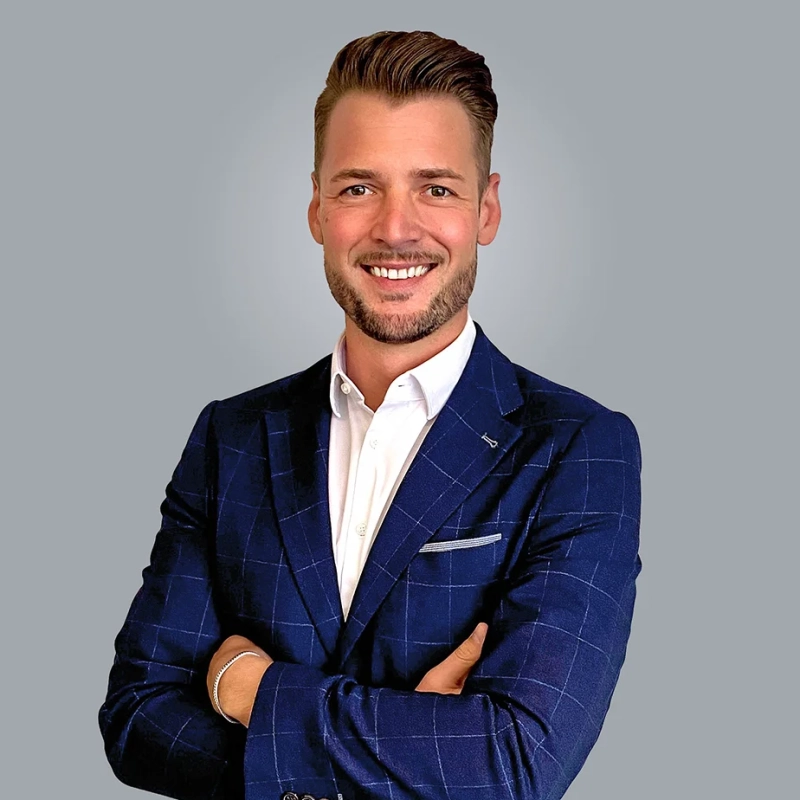
I Will Be Happy to Help You
Philipp Seibald
Head of Business Development