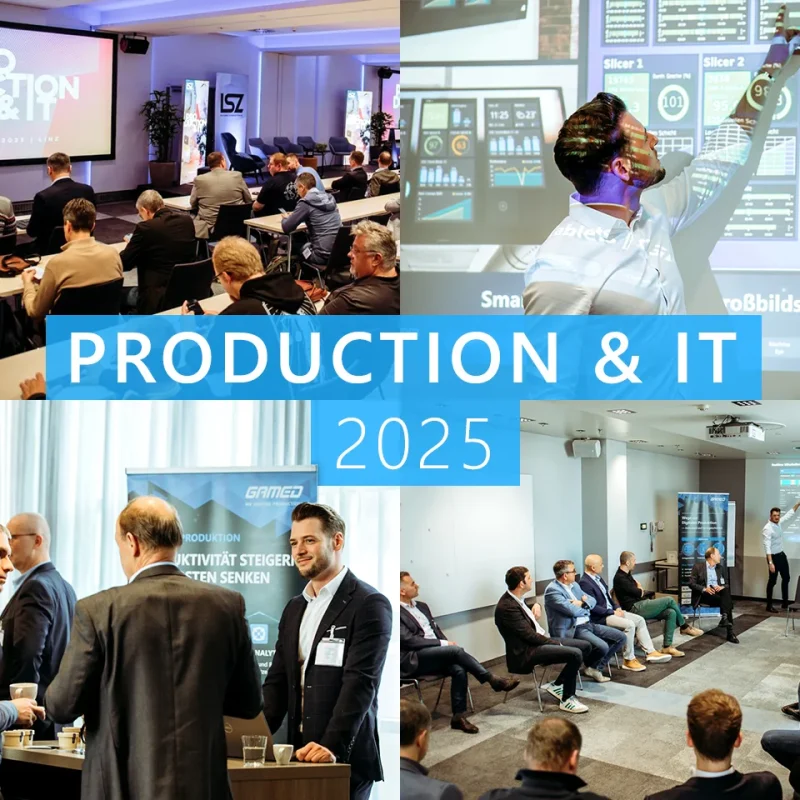
Philipp Seibald
16. Februar 2024
Mit Check 4.0 bieten wir Ihnen eine Roadmap zur Umsetzung der Digitalen Produktion, individuell auf Ihre Situation abgestimmt. Gemeinsam definieren wir das Ziel: Reduktion von Verschwendung und Bestand, Erhöhung der Transparenz und Erfüllung von Planvorgaben, Reduktion von Papier im Prozess und manuellem Aufwand sowie Automatisierung im Allgemeinen sind gängige Treiber der Digitalisierung in der Produktion.
Zur Feststellung des Ist-Stands erheben wir in Ihrem Unternehmen die IT-Strukturen und den Digitalisierungslevel einzelner Fachbereiche. Anhand von Referenzmodellen bewerten wir die Untersuchungsergebnisse und erstellen daraus Ihren Masterplan zur Zielerreichung – unser Vorschlag in abgestimmten Schritten zu den Fragen: Wo werden welche Daten automatisch erfasst? Wie werden die Daten automatisch integriert, ausgewertet und visualisiert? Welche Prozesse werden automatisiert?
Wird der Masterplan von der Geschäftsleitung und den Fachbereichen mitgetragen, empfehlen wir zur Umsetzung ein Bottom-Up-Vorgehen: von der Maschinenebene über den Fertigungsablauf bis zur Einbindung aller beteiligten Fachbereiche.
In der ersten Stufe steht die Beseitigung von Produktivitätskillern an den Anlagen und insbesondere an Engpassmaschinen im Fokus. Das OEE-Analyseverfahren in digitaler Form liefert flächendeckende Transparenz zu allen wichtigen Leistungskennzahlen der Anlagen und zeigt auf, wo Potenziale für beherrschte, planbare Prozesse liegen.
Erreichen die Anlagen die benötigte Performance stabil, wird in der nächsten Stufe der gesamte Fertigungsablauf gesteuert und optimiert. Grundlage dazu ist eine auftragsorientierte oder stückbezogene Materialverfolgung. Danach werden unterstützende Fachbereiche wie Qualitätssicherung, Werkzeugbau, Logistik und Instandhaltung in einen durchgängigen Informationsverbund integriert. Koordinierung der operativen Abläufe sowie die Analyse von Prozess- und Qualitätsdaten zur Fehleranalyse und -prävention stehen hier im Mittelpunkt.
Visualisierung am Arbeitsplatz ist ein wichtiger Beitrag zur Lean-Kultur und Prozessbeherrschung. Großanzeigen/TVs im Shopfloor sowie mobile Geräte bieten Führungskräften Zugriff auf aktuelle Kennzahlen und wichtige Entwicklungen im Betrieb.
Machine Eye und Cross Plant Reporting System sind Web-basierte Software-Systeme, mit der Sie Info-Boards und Datencockpits selbst gestalten. Die Anzeigen auf Smartphone, Tablet oder PC erfolgen in Echtzeit und über offene Schnittstellen werden Daten von externen IT-Systemen übernommen.
Ein zentrales Thema ist die automatische Ermittlung der Produktivität und Leistungskennzahlen Ihrer Anlagen. Die automatische Arbeitsweise entlastet Ihre Mitarbeiter und liefert genaue Ergebnisse in Echtzeit. Verschiedene Ansichten, von aktuellen schichtbezogenen Daten über Managementinformationen bis zu standortübergreifenden Cockpits unterstützen unterschiedliche Benutzer im Unternehmen.
OEE Analyser ist ein System zur Maschinendatenerfassung um die Produktivität und Leistungskennzahlen Ihrer Anlagen zu ermitteln. Ob Einzelmaschine, Fertigungslinie oder Batchanlage, das Produkt ist universell nutzbar.
Wo stehen die Fertigungsaufträge und werden sie rechtzeitig fertig? Die Auftragsverfolgung liefert ein aktuelles digitales Abbild des Fertigungsprozesses: wie ist der Bearbeitungsfortschritt, welcher Auftrag bzw. welches Teil läuft gerade an einer Maschine, wo liegt welches Material, usw. Process Master ist ein Framework um Ihre Aufträge integriert zu managen und zu verfolgen. Die vom ERP- oder Planungssystem übernommenen Aufträge können um technologische Vorschriften und Prüfanweisungen ergänzt werden. Die Auftragsverfolgung visualisiert den Ablauf für Produktionsverantwortliche, liefert Ergebnisdaten an die ERP/Planungsebene und steuert den Materialfluss sowie die Übertragung von spezifischen Programmen an die Steuerungsebene.
Bei Bedarf bieten auch wir Lösungen für die Produktionsfeinplanung an.
Neue Einsichten gewinnen, Qualität nachweisen, Fehlerursachen erkennen – Prozessdaten und deren Analyse bieten großes Potenzial. Anlagen-, produkt- oder qualitätsbezogene Prozessdaten sowie Verbrauchswerte werden in Steuerungen oder SCADA-Systemen erfasst. Daten aus verteilten Systemen zusammenzuführen, aufzubereiten, entsprechend zu verspeichern und zu aggregieren sind die ersten Schritte der Datenanalyse.
DataBridge ist ein konfigurierbares Kommunikationssystem um diverse Steuerungs- und IT-Systeme auf Basis OPC, TCP oder Datenbankebene zu integrieren.
VisualDataXplorer ist ein Datenanalysesystem. Die intuitive Benutzerführung und sorgfältige Auswahl der Analyseverfahren erlauben es schnell und effizient Einsicht zu gewinnen. Mit unserer Erfahrung in Datenanalyseframeworks wie R oder Python unterstützen wir Sie bei der Anwendung.
Neben dem Gewinn neuer Erkenntnisse, gilt es datengetriebene Modelle zur Steuerung von Anlagen und Prozessen zu nutzen. Zu diesem Zweck finden IIoT-Plattformen und Edge-Devices Anwendung.
In Zeiten knapper Personalressourcen stellt die Erhaltung einer hohen Anlagenverfügbarkeit und intakten Infrastruktur Unternehmen vor große Herausforderungen. Zertifizierte Unternehmen (z.B. nach IATF 16949) müssen darüber hinaus regelmäßig und detailliert ihre Serviceleistungen nachweisen. Maintenance unterstützt Sie dabei, derartige Anforderungen im Anlagenmanagement zu meistern und TPM optimal umzusetzen. Neue Technologien wie mobile Geräte unterstützen Servicetechniker im Anlagenfeld, in der Werkstätte und im Lager.